Factory-Built Housing Can Be Better than You Think
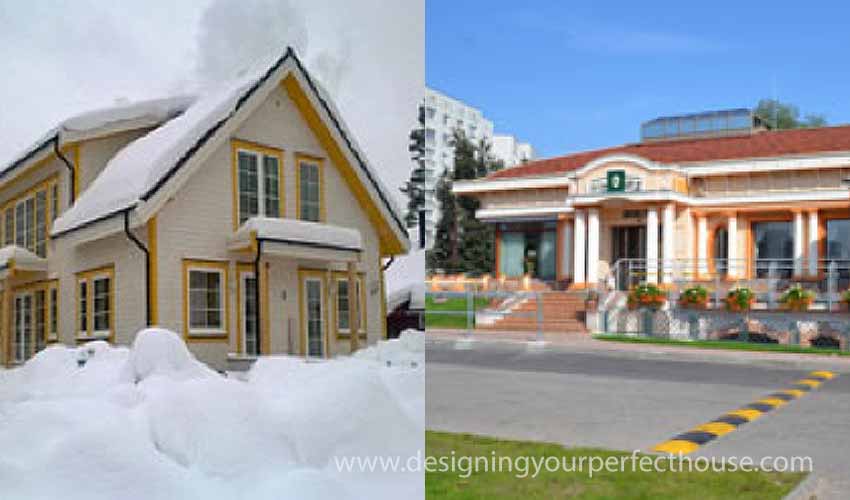
If you are like most Americans, when you hear the term “Factory-Built” or “Modular” housing, you probably think of what you see rolling down the highway on a truck with the house-wrap flapping in the breeze. You think of a tiny house that is just a small step up from a trailer. You think of a “double wide.” Your impression is that a modular house is a low-cost factory-built dwelling that arrives on-site by truck and is scattered across the rural parts of the country. But factory-built housing can be much more than that. And the quality can easily exceed the quality of even the best built “site-built” house.
What’s the Difference Between Factory Built Housing and Modular Housing?
Modular housing usually refers to houses that are standard plans and designs that are repeated, one unit after the next. Factory built housing, on the other hand, refers to any kind of house that is assembled in components manufactured in a factory and assembled on site. There are varying degrees of factory built house construction. The most efficient and customizable is a panelizing method where the walls and roofs are manufactured in panel section and assembled on site. Modular housing typical involves entire rooms or segments of the house being assembled in the factory and then shipped to the site.
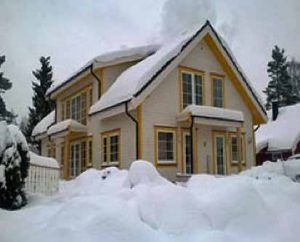
Factory built housing does not automatically consist of inferior materials. Absolutely not. The quality of the materials and components can be at whatever level you specify. Factory-built houses can match anything you could have with a site-built house. But not merely match the quality, a factory-built house can exceed site-built houses in several ways.
Factory Built Housing Has Advantages
It mystifies me why more housing is not factory built. There are such clear advantages when compared to the traditional methods of “stick building” on site in all kinds of weather conditions. Here are some advantages to factory built housing.
First, factory-built housing is assembled in a controlled environment under roof.
Rain or snow can never sit on the wood. Temperatures never vary more than a degree or two so the materials don’t expand or contract. The construction personnel can work at peak efficiency. Building inside a controlled environment makes good sense. Just think about this. Would you want to buy a new BMW and have a crew show up in your driveway with cartons of parts and start assembling your car there? My guess is the rain, snow, and mud getting inside the car would be more than a little distressing.
Second, the work can be done more efficiently.
This is because the materials in a factory are moved to the worker. When building on-site, the workers have to move every piece of building material to the location where it is to be used. Nearly every piece of the house gets moved several times. There are no “rain days” in a factory. You never losing work days to weather. Even on days when work can be done, if it is raining, or freezing cold, or swelteringly hot, no one can work at their best. Working outdoors is simply less efficient. Work in a factory is always done efficiently. Optimum temperatures, optimum lighting, and safe conditions means you have a construction schedule that is predictable and faster.
Third, the cutting and fitting of materials will be better under factory conditions.
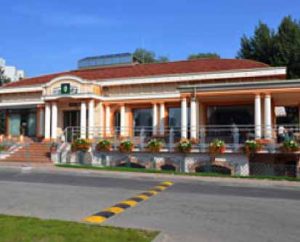
Lasers and jigs are used to ensure accurate measurements and the “squareness” of connections. Think of the BMW assembling in your driveway again if you want a disconcerting visual of skilled metalsmiths cutting and hammering the body of the car. No matter how good they were, their precision can never match what they could achieve in a workshop. The factory is their workshop.
Fourth is safety
Construction sites are always ranked among the most dangerous workplaces. Dangerous equipment, heavy materials moving around, and workers working high above the ground combine to create serious risks. Workplace safety is always a priority, but it is simply impossible to make an outdoor building site be as safe as a factory setting.
We Need More Factory Built Housing in the United States
We are strongly considering using a factory-built panelizing system for the construction of the house I am designing in Latvia. We’re talking to Ivars Reinhards and his company, WWL Houses. Now we just need a company like his to begin factory building houses in the United States.
Follow the Latvia house progress:
- Architecture Traveling in Latvia
- Peteris Blum and the Wooden Architecture of Latvia
- Latvian Symbols in Art and Architecture
- The Hand Crafted Heritage in Latvia
I hope this information is helpful to you. You might want to get yourself a copy of my best-seller, Designing Your Perfect House. It is chockfull of valuable tips and advice that will save you many times the cost of the book on your house building or remodeling project. You might also like The Well-Centered Home: Simple Steps to Increase Mindfulness, Self-Awareness, and Happiness Where You Live. It will show you how to make your home a happy place.